Many of the electronics and electrical components that make modern life possible and comfortable — laptops, smartphones, car batteries — are dependent on a handful of valuable materials. When one of these items returns to a recycling facility at the end of its life, the copper, gold, silver and maybe a few other precious metals will be harvested from the device before the rest is incinerated, becoming lost forever. Recycling efforts thus far have focused primarily on these most valuable elements and on recapturing them as quickly as possible and with the least amount of effort, even if that means creating pollution, losing other materials and degrading the recaptured ones in the process.
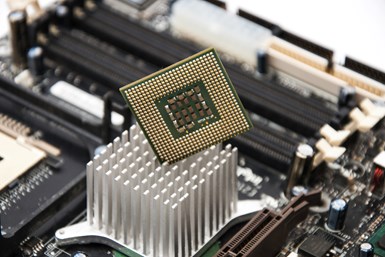
Circuit boards and other electrical components are often not recycled in their entirety, with some elements extracted while less-valuable materials end up incinerated. Photo Credit: Stock
Reco E-Waste takes a different approach aimed at less harmful and more complete recycling. The Munich, Germany-based company (part of Reco Ventures) has developed what it says is a lossless process for recapturing precious and rare-earth materials and transforming them into high-purity feedstock, including very fine and consistent powder for additive manufacturing. The method requires no heat, no induction and no chemicals; the result is a one-to-one relationship between the input and the output for most materials.
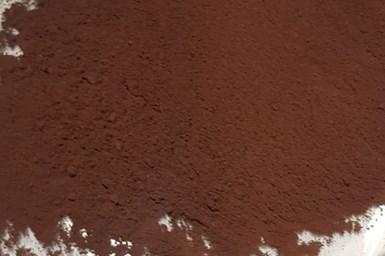
Reco E-Waste aims for more complete extraction from electronics and other components, recycling these materials into powders suitable for additive manufacturing. Photo Credit: Reco E-Waste
“Of course it takes longer,” says Rudolf von Stokar, the company’s owner and founder, describing the various steps needed to extract each of the materials individually. “The effort is high, but the output is very satisfying.” That output is high-quality, consistent and valuable materials suitable for laser powder bed fusion (LPBF), one of the most flexible manufacturing processes currently available. But the end result is also sustainable and conflict-free as it comes from secondary sources — an important point in efforts to localize supply chains, reduce reliance on material sources abroad, and avoid contributing to human rights violations in nations that have traditionally mined these materials.
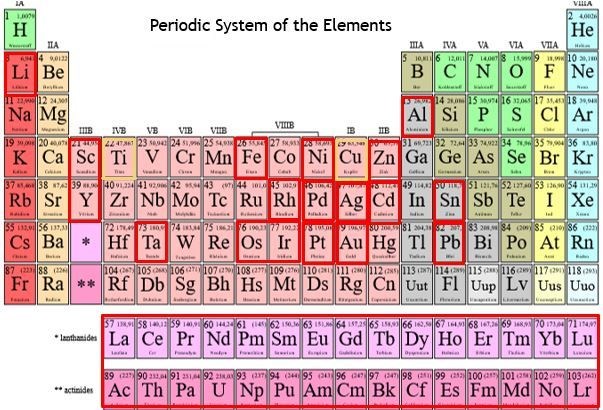
Most industrial recyclers focus on recovering just a handful of the most lucrative materials. Reco E-Waste aims to capture all the elements outlined in red on this periodic table. Image: Edited from Wikimedia Commons
Recapturing E-Waste Materials
Rather than fast and easy, Reco E-Waste from the beginning has prioritized completeness. Nothing from the original CPU, hard drive, computer mouse or laptop is wasted if the company can help it. For most metal materials, the conversion rate is 1-to-1 from input to output. The process looks like this:
- Devices are collected, cleaned and disassembled; at this stage nonmetal elements such as plastics are separated out into other recycling streams. Metals are tested to determine their makeup before moving into the extraction process.
- Metals are extracted one by one. “This is production reversed,” von Stokar says. A series of catalytic reactions dialed in for each element separates them one at a time. A part might be stripped of all its gold, then its copper, then its aluminum, for instance. Catalysts used in these reactions are food grade and don’t contaminate the wastewater.
- Each recovered material is converted into pellets, then mechanically sized down as needed. A combination of cleaning and sieving steps sequentially improves material purity while reducing powder particle size. Reco E-Waste has successfully produced powders as small as 20 nanometers in diameter. These very fine powders are of particular interest for medical additive manufacturing, where powder diameter translates into surface quality and ease of cleaning for an end-use medical device.
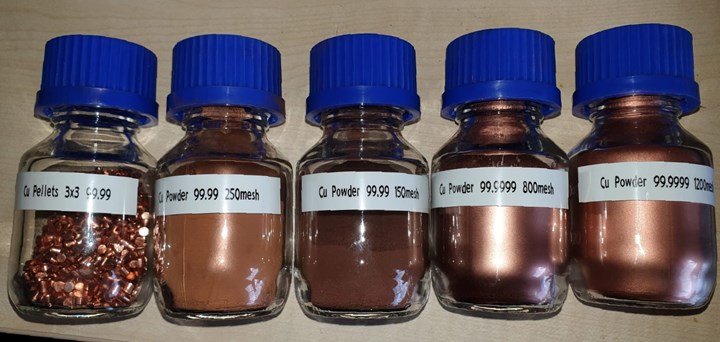
One of Reco’s goals is to produce “the highest possible purity in the smallest possible size” of powders, von Stokar says. Moving from left to right, each bottle pictured here reflects additional processing needed to take the copper pellets in the first bottle down to finer and finer AM-ready powders. Photo Credit: Reco E-Waste
With three facilities in Germany, Reco E-Waste is currently capable of processing up to 3 tons of raw material and producing between 500 and 1,500 kg of metal powder each day. Materials currently being converted are primarily copper, aluminum and nickel, but gold, lithium, palladium, silver, platinum and other metals commonly found in electronics are being recaptured as well. Right now, much of its feedstock is free — discarded e-waste either donated or sought out by the company to divert it from conventional recycling or the landfill. In some cases Reco is even stockpiling some items it isn’t yet processing, like old TVs and radios, in anticipation of coming demand for the materials they contain.
(Interestingly, the materials captured need not be in demand for new products. At one point Reco began collecting “power counters,” the old plastic enclosures that used to house the electricity meters in German households. The particular plastic is no longer produced or used in new products, but it is still in demand because it was also used to mold headlights in older automobiles. The classic car market turned out to be a destination for this seemingly obsolete material.)
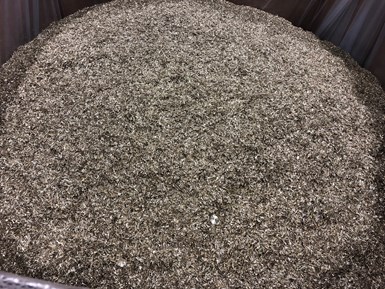
Reco is working to expand its services beyond electronics into materials such as steel and titanium. Industrial waste like these stainless steel machining chips are one potential source of feedstock. Photo Credit: Derek Korn
Ultimately, the company aims to offer a “full range” of materials as a one-stop shop for high-quality powders for additive manufacturing. This will mean expanding into new metals outside the electrical realm, including steel and titanium. It will mean bringing lab capacity in-house. It will mean building out staff, facilities and eventually expanding internationally.
Part of the strategy going forward too will be more formalized relationships with manufacturers, to capture and recycle materials in a cradle-to-cradle fashion. Reco E-Waste already has some industrial customers that engage with the company in this circular economy model. Process waste, scrapped components or used products can be turned over to Reco to be converted into 3D printing materials that those customers can then buy back if they choose. Whether the material literally returns to the manufacturer or not is less important, however, than keeping the existing material in play wherever it can be used.
Related Content
How to Build 10,000+ Shot Molds in Hours
Rapid tooling isn’t so rapid when it takes days to 3D print a metal mold, and then you still must machine it to reach the necessary tolerances. With Nexa3D’s polymer process you can print a mold in hours that is prototype or production ready and can last for more than 10,000 shots.
Read MorePostprocessing Steps and Costs for Metal 3D Printing
When your metal part is done 3D printing, you just pull it out of the machine and start using it, right? Not exactly.
Read More3D Printed Cold Plate for an Electric Race Car: The Cool Parts Show #51
An unconventional lattice design and biomimicry are key to the performance of this fluid-cooled heat exchanger for a battery-powered race car.
Read MorePossibilities From Electroplating 3D Printed Plastic Parts
Adding layers of nickel or copper to 3D printed polymer can impart desired properties such as electrical conductivity, EMI shielding, abrasion resistance and improved strength — approaching and even exceeding 3D printed metal, according to RePliForm.
Read MoreRead Next
Getting to a Circular Model for Metal Powders Makes AM More Sustainable
6K’s UniMelt process offers efficiency and control in the production of metal powders for additive manufacturing. But more than that, it is a home for unused and oversized powder, metal scrap and more that can close the loop on metals.
Read More3D Printing with Renewable Materials, Frugally Applied (Video #1)
Part of our 3D Printing and the Circular Economy series, this video explores the ways that AM supports more sustainable material choices.
Read MoreRounding Out the Circular Economy With Material Take-Back Programs: AM Radio #6A
One of the most difficult steps in the circular economy is going from product back to new material. On this episode of AM Radio, Julia Hider and Stephanie Hendrixson discuss how material take-back programs can help solve this challenge.
Read More