“Castings offer a much bigger opportunity than we once gave credit to,” says Mark Douglass, business development manager with Lincoln Electric Additive Solutions. He helps to lead a facility in Euclid, Ohio, that runs 18 wire arc additive manufacturing (WAAM) robots for 3D printing via metal deposition, offering production capacity for large metal components that might otherwise be cast. The significance of this opportunity became apparent during the height of covid’s disruptions, as supply chains were broken and stretched. Additive manufacturing (AM) can deliver large metal parts within three or four weeks where the lead time to obtain the same part via casting might easily be five times as long, and longer during a time of disruption.
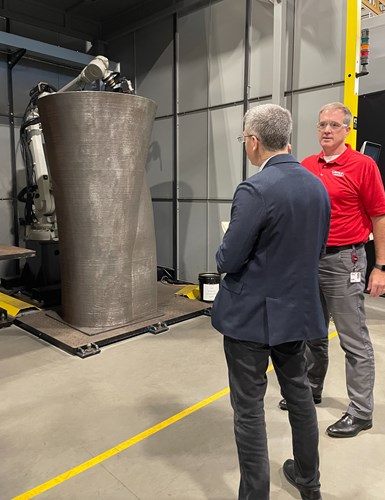
This part in work at Lincoln Electric’s AM facility in Euclid, Ohio, is unusual — a component of a sculpture by artist Jenny Sabin for the University of Nebraska Medical Center — but it illustrates the freedom of WAAM to produce very large structures. Large parts like this can be welded together to produce very larger forms because, as Mark Douglass (right) explains, the wire arc additive manufacturing process is essentially welding anyway.
But what is the value of that speed?
Douglass says the lack of a precise answer to this question might be the chief remaining obstacle to seeing more widespread use of additive manufacturing as a casting alternative.
Indeed, a similar uncertainty surrounds the design freedom of AM, and the elaborate part geometries and material combinations it can achieve, along with the chance to change design at will mid-production. What is the way to value all this freedom in rationalizing the production process choice? The freedom of additive is so much greater than that of conventional processes, and the lead time potentially so much shorter, that industry generally does not yet have measures for valuing these opportunities.
There are other limitations to be sure. Material cost is one; the wire in wire arc additive must be delivered in a way that is tailored to this process. As a result, “For runs of hundreds or thousands of parts, we are not cost competitive,” Douglass says. Casting wins on volume. But where the quantity is instead around ten parts, additive does tend to win — and many production parts currently made through casting are made in these quantities. The freedom additive brings to easily vary geometry into more diverse part families promises to bring even more work over time into quantities within this range.
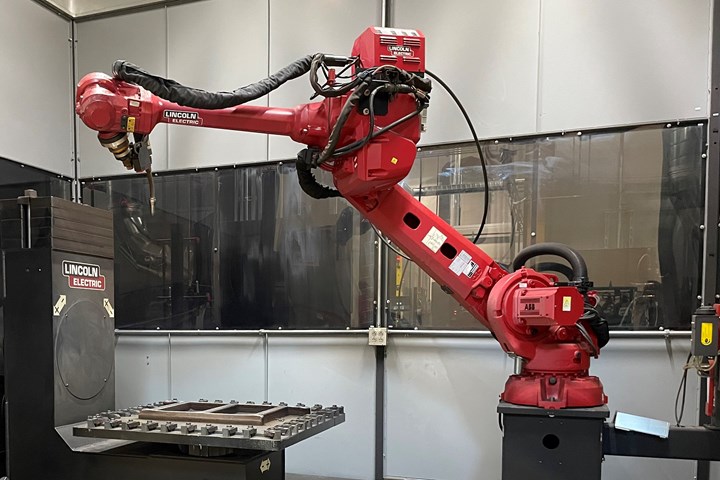
The Cleveland-area Additive Solutions facility currently runs 18 robots performing WAAM. As this photo captures, a robot offers considerable freedom over an enclosed machine when it comes to reaching around the work space to deposit material at different angles.
Meanwhile, the welded part produced through metal deposition is more consistent in internal quality, with properties nearer to wrought material. The technology is proven and ready.
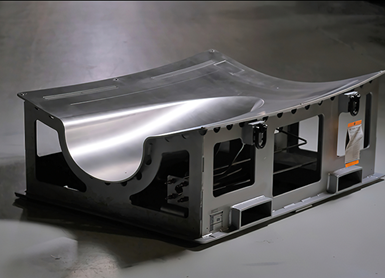
Tooling, particularly large tools for the aircraft industry, represents perhaps the leading application for WAAM today. Seen here is a composites layup tool in which the working surface was 3D printed from Invar.
And working, Douglass says. The Cleveland-area facility is generally busy, albeit at present often making tools. Tooling is the area that has already made this conceptual leap. The WAAM systems are employed by aerospace and other manufacturers to make tools for metalforming, molding and composites lay-up. In tooling, it is easier to embrace a new manufacturing process, plus easier to value the gain of a benefit like shorter lead time (which leads to making parts with the needed tool that much faster). Therefore, large-format robotic WAAM in Cleveland is following the same course other 3D printing processes in other materials at other scales have also taken: Tooling is charting the course that production will follow.
The difference with WAAM is that the process is already so well accepted and known, because it is based on an operation manufacturers have employed for well over a century. “At the end of the day it’s welding,” Douglass says. “Except it’s not.” That is, the considerations include, but also extend beyond, what is typical for established welding.
Different From Welding
Lincoln Electric has specialized in welding for just over 125 years. (The pandemic precluded an anniversary celebration.) The company has large customers that rely on it for welding systems, including well known heavy-industry OEMs, that are also interested in realizing the flexibility and cost-saving potential of additive. In addition, Lincoln Electric is notable for developing and producing all the components of welding systems, including power supplies, torches and materials, within its own organization.
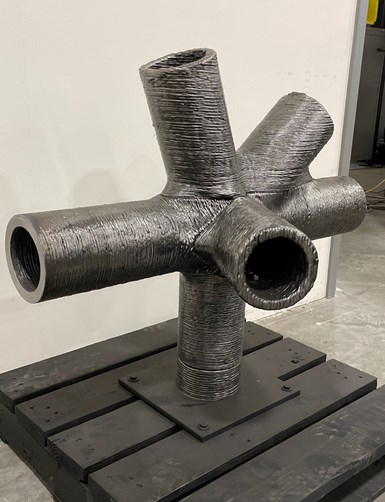
Note how the layer lines are not all parallel. Robotic deposition allows for building different features at different angles within the same cycle. This part is a demonstration piece exploring the possibility of using joints made via AM as an alternative to fabricating joints when building offshore oil platforms.
The system approach is valuable for succeeding in AM. WAAM is welding, but it is continuous welding involving stacking carefully placed weld beads. This has implications for every aspect of the WAAM process, including deposition, metallurgy, robotics and even finish machining.
And software. Deposition via welding is not just a matter of tool path (or torch pass), but also is affected by the frequency and amplitude of current wave forms. “A traditional CAM software company is unlikely to develop this kind of capability,” says Douglass, but Lincoln has developed and continues to develop software focused on WAAM.
Material is another important aspect. Standard weld material will work in WAAM, except it won’t. “You want to draw from a big wire package or else you will be changing a lot of spools. Then, how do you correct the twist of the wire coming out of the drum so that it feeds well enough for controlled deposition?” Solving these problems is part of material optimization for additive.
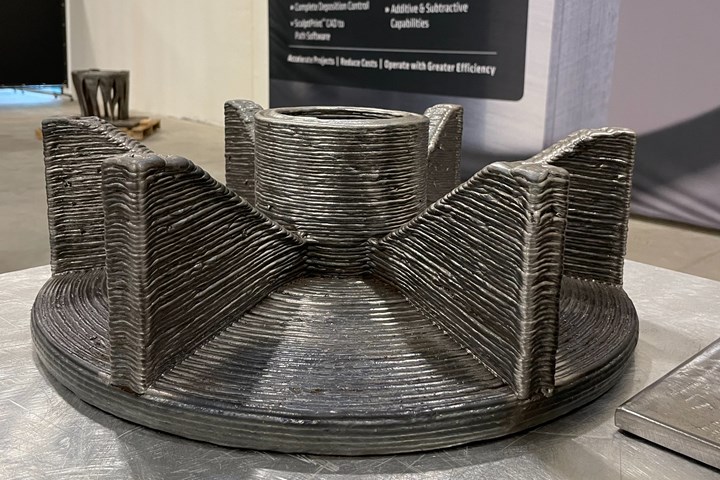
This component is an example of another promising application: replacements parts for large machine components.
Lincoln Electric performs AM part making in-house as well. The current state of AM acceptance and application requires this, Douglass says. “We have to use this technology in order to keep improving it, and we need to keep succeeding with it to grow the market.” Also, potential users who might invest in having their own WAAM capability cannot yet justify (or necessarily find) personnel with WAAM expertise. The existence of Lincoln Electric Additive Solutions therefore demonstrates another way — that is, making parts instead of selling systems — that WAAM is different from welding.
Nearby Supply
And did I mention the parts are made in Ohio? On the author’s part, a bit of Ohio pride goes into stressing this point. However, the point also illustrates just how short the supply chain is liable to be for parts made through WAAM. As contrasted with large castings that might travel from a foundry overseas, the metal 3D printed parts are made and machined entirely in the Midwest, for shipping to customers located in the same region. “Time to market is one of the key benefits of this capability,” Douglass says.
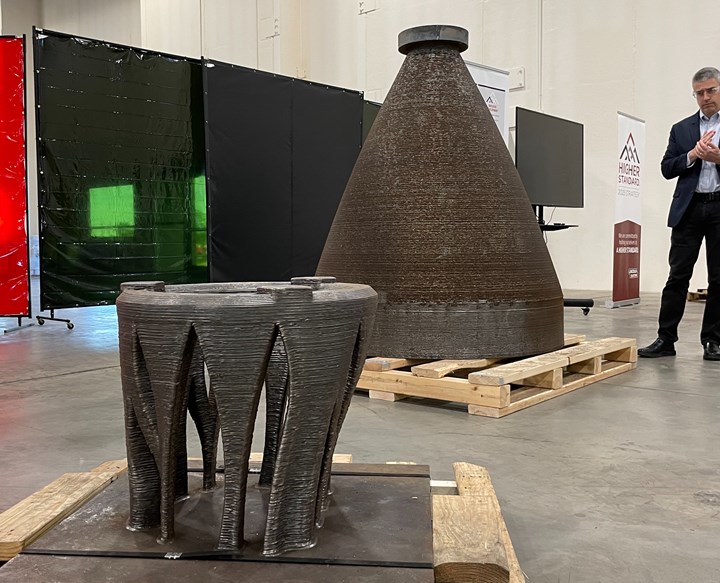
To give the robot just enough height to reach the top of the part in the background and print it all in once cycle, Lincoln Electric first 3D printed the pedestal in the foreground on which the robot was mounted.
One buyer of large, relatively low-quantity castings is already convinced. For pressure vessels currently made through casting, the 16- to 18-week delay currently accepted to obtain the casting can be replaced by four to five weeks to deliver the part complete through WAAM followed by machining, with superior metallurgical properties thrown in.
The problem: Vessels made according to ASME standards for these components must use welding procedures qualified to a specific set of codes that do not offer a method to qualify the welding procedures for WAAM.
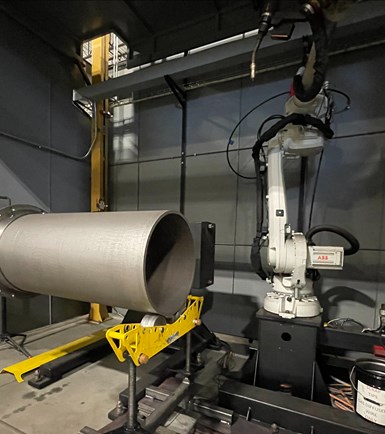
WAAM is like welding, but not. One difference: Welding does not call for the continuous deposition AM does. This test setup explores that difference; 3D printing on this pipe is part of an evaluation of nozzle life.
The standards are important, and the pressure vessel maker needs to abide by them. Industry standards serve the vital role of setting a shared industry baseline for defining expected part performance and quality. For WAAM to be used, it has to somehow abide by them.
And, as this article was nearing completion, Lincoln Electric was able to announce headway. Thanks in part to the participation of a Lincoln Electric Additive Solutions team member in the discussions, the relevant ASME codes have now added a means to qualify gas metal arc additive manufacturing. Procedures for WAAM with a mild steel alloy have already been qualified according to this system.
Advancing AM right now requires this kind of engagement with, and acceptance within, relevant industry systems and standards, Douglass says. It is not so much a matter of technology development anymore. That is still proceeding, but the technologies are mature enough to perform, including in series production. The larger challenge now relates to mindsets and expectations; the ways we see and value benefits; and the frameworks industries use to understand and characterize their production choices.
Related Content
Possibilities From Electroplating 3D Printed Plastic Parts
Adding layers of nickel or copper to 3D printed polymer can impart desired properties such as electrical conductivity, EMI shielding, abrasion resistance and improved strength — approaching and even exceeding 3D printed metal, according to RePliForm.
Read MoreVulcanForms Is Forging a New Model for Large-Scale Production (and It's More Than 3D Printing)
The MIT spinout leverages proprietary high-power laser powder bed fusion alongside machining in the context of digitized, cost-effective and “maniacally focused” production.
Read MoreWhat is Powder Bed Fusion 3D Printing?
Whether in metal or polymer, with a laser or an electron beam, powder bed fusion (PBF) is one of the most widely used 3D printing techniques.
Read MoreHow to Build 10,000+ Shot Molds in Hours
Rapid tooling isn’t so rapid when it takes days to 3D print a metal mold, and then you still must machine it to reach the necessary tolerances. With Nexa3D’s polymer process you can print a mold in hours that is prototype or production ready and can last for more than 10,000 shots.
Read MoreRead Next
Three Cool Uses for Directed Energy Deposition
Most machining professionals don’t like to admit that they ever make mistakes, but every now and then wouldn’t it be nice to have an “eraser” to go back and repair a gouge or fix a nicked edge? Or maybe you took off a bit too much material on that last machining pass and you’d like to add it back? Well, directed energy deposition (DED) enables you to do that and more.
Read MoreThe Hidden Complexities of Wire Arc Additive Manufacturing
Lincoln Electric Additive Solutions’ robotic metal 3D printing process is a choreographed dance between welding, robots, automation, heat management and machining. The new venture may have a distinct advantage in the field: its parent company’s 125 year-old legacy.
Read MoreThe Promise of Robotic Metal Additive Manufacturing
Addere’s robot-based laser system builds using standard weld wire. The company was spawned from a robot integrator, and that background has been valuable for both overcoming the challenges and perceiving the possibilities of using a robot for metal 3D printing.
Read More